The Science Behind Porosity: A Comprehensive Overview for Welders and Fabricators
Understanding the detailed mechanisms behind porosity in welding is crucial for welders and producers striving for impressive craftsmanship. From the composition of the base products to the details of the welding process itself, a wide range of variables conspire to either exacerbate or reduce the presence of porosity.
Comprehending Porosity in Welding
FIRST SENTENCE:
Examination of porosity in welding reveals crucial insights right into the honesty and quality of the weld joint. Porosity, characterized by the presence of dental caries or gaps within the weld steel, is a typical problem in welding procedures. These gaps, otherwise effectively resolved, can jeopardize the architectural integrity and mechanical residential or commercial properties of the weld, causing prospective failures in the ended up item.

To find and evaluate porosity, non-destructive screening techniques such as ultrasonic testing or X-ray inspection are usually utilized. These methods enable the identification of interior problems without compromising the honesty of the weld. By examining the size, form, and distribution of porosity within a weld, welders can make informed decisions to improve their welding procedures and accomplish sounder weld joints.

Aspects Affecting Porosity Development
The occurrence of porosity in welding is affected by a myriad of aspects, ranging from gas shielding efficiency to the complexities of welding criterion settings. One critical aspect adding to porosity formation is insufficient gas securing. When the securing gas, normally argon or CO2, is not effectively covering the weld pool, atmospheric gases like oxygen and nitrogen can pollute the molten steel, bring about porosity. In addition, the cleanliness of the base materials plays a significant role. Impurities such as corrosion, oil, or wetness can evaporate during welding, developing gas pockets my website within the weld. Welding specifications, consisting of voltage, present, travel rate, and electrode kind, also influence porosity development. Using inappropriate setups can produce extreme spatter or heat input, which subsequently can result in porosity. Moreover, the welding technique used, such as gas steel arc welding (GMAW) or protected steel arc welding (SMAW), can influence porosity formation as a result of variations in warmth distribution and gas protection. Recognizing and controlling these aspects are necessary for reducing porosity in welding procedures.
Impacts of Porosity on Weld Quality
The existence of porosity also weakens the weld's resistance to deterioration, as the caught air or gases within the spaces can respond with the surrounding setting, leading to degradation over time. In addition, porosity can impede the weld's ability to hold up against stress or impact, further jeopardizing the general quality and dependability of the welded framework. In important applications such as aerospace, automobile, or structural constructions, where security and longevity are extremely important, the damaging results of porosity on weld top quality can have severe consequences, emphasizing the relevance of lessening porosity with appropriate welding techniques and treatments.
Strategies to Reduce Porosity
Additionally, using the suitable welding specifications, such as the proper voltage, current, and take a trip rate, is crucial in stopping porosity. Preserving a constant arc size and angle throughout welding also aids lower the possibility of porosity.

Utilizing the ideal welding strategy, such as back-stepping or utilizing a weaving motion, can additionally assist distribute warmth uniformly and reduce the opportunities of porosity formation. By implementing these techniques, welders can properly reduce porosity and generate top notch welded joints.
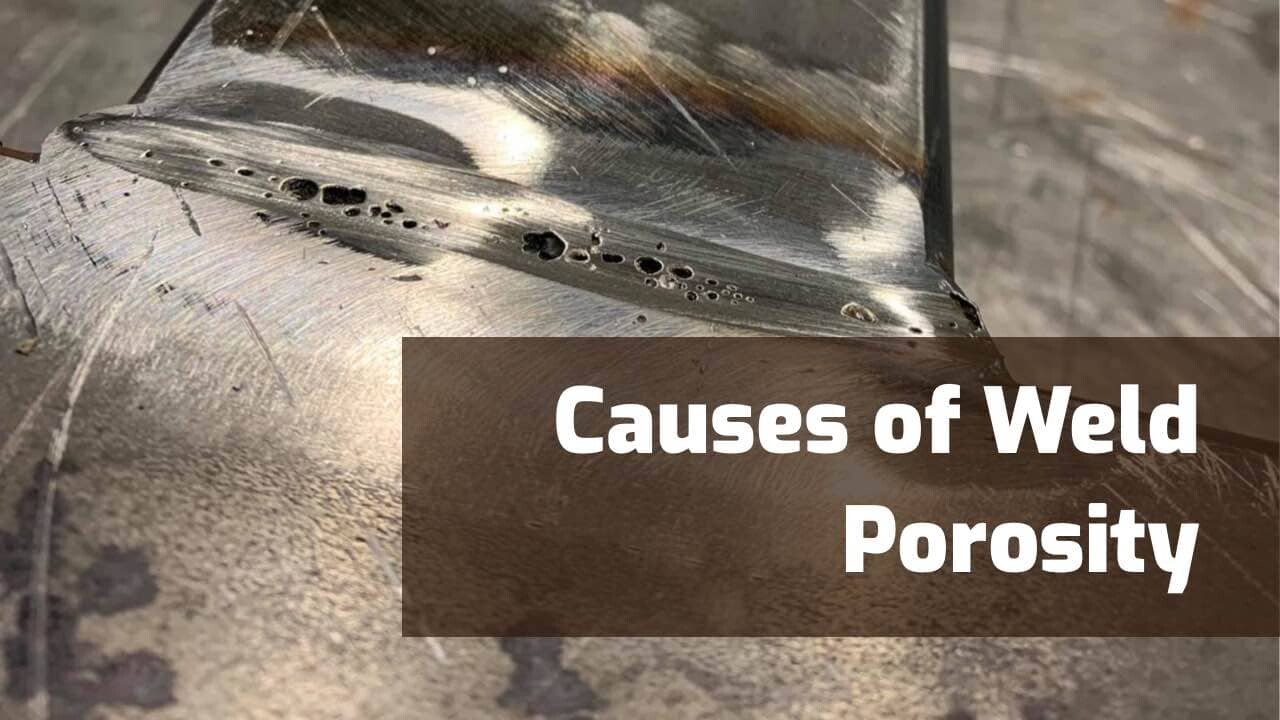
Advanced Solutions for Porosity Control
Implementing innovative technologies and ingenious methods plays a crucial function in achieving premium control over porosity in welding processes. In addition, utilizing advanced welding methods such as pulsed MIG welding or modified environment welding can additionally assist alleviate porosity concerns.
Another sophisticated option involves the use of sophisticated welding tools. For example, using devices with integrated attributes like waveform control and sophisticated power sources can improve weld high quality and decrease porosity risks. The application of automated welding systems with accurate control visit site over criteria can significantly minimize porosity flaws.
In addition, including innovative surveillance and inspection technologies such as real-time X-ray imaging or automated ultrasonic testing can help in finding porosity early in the welding process, enabling immediate corrective activities. Generally, integrating these advanced solutions can greatly boost porosity control and boost the overall high quality of bonded parts.
Final Thought
In conclusion, recognizing the science behind porosity in welding is essential for welders content and producers to generate premium welds - What is Porosity. Advanced remedies for porosity control can additionally boost the welding process and guarantee a solid and reputable weld.